A facility on the Gulf Coast had an out of service tank that once contained Pyrolysis Gasoline (Pygas), but had recently been used to store various waste streams and contaminated water.
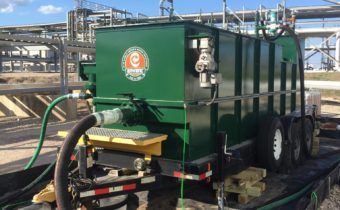
A facility on the Gulf Coast had an out of service tank that once contained Pyrolysis Gasoline (Pygas), but had recently been used to store various waste streams and contaminated water.
A refinery conducted a turnaround on a Hydrocracker unit in the Deer Park area, and they required a complete turnaround solution. Having worked with Envent before, the customer knew that we could solve all of their needs.
A refinery customer planned a turnaround for their Fluidic Catalytic Cracking Unit and was in need of turnaround service support. Because Envent has demonstrated the ability to help our customers meet the new, stricter emission limits imposed by the new Petroleum Refinery Sector Risk & Technology Review (RSR) regulations, the refinery knew they were getting the best.
Port Arthur refinery customer planned a turnaround for their 4 Drum Delayed Coker Unit. Due to the stricter emission limits imposed by the new Petroleum Refinery Sector Risk & Technology Review (RSR) regulations, the refinery needed Envent’s help.
Deer Park refinery facility required a flareless turnaround due to the new Petroleum Refinery Sector Risk & Technology Review (RSR) regulations. In order to remain in compliance and shorten the duration of the decommissioning phase, Envent was called upon to depressure the unit.
An underground natural gas pipeline was discovered leaking in a residential area. Although the pipeline owner quickly fixed the leak, much of the soil had become saturated with odorized natural gas. In order to protect the nearby residences and shops, the company needed an engineered solution to degas the soil as quickly as possible.
A tank farm had collected over 600,000 gallons of storm water runoff. The storm water needed to be treated for total suspended solids, oil and grease, benzene, toluene, ethylene and xylene. The treated water would be discharged directly into Fort Worth’s sewer system.
A Westlake Louisiana refinery required vapor control on their tank while a robotic crawler made entry into the tank. The company was trying to recover $10,000,000 worth of catalyst that had carried over from their Catalytic Cracking Unit. Envent was also requested to provide vacuum rated carbon containers.
A refinery with a sour water tank high in H2S needed vapor control provided during a turnaround while maintenance was done in the surrounding area. The H2S needed to be reduced to a safe level while the vapors were treated and vented to atmosphere. Successfully reduced the H2S emissions in the area so turnaround could continue.
A large Texas refinery was in need for a long term vapor control solution for their refinery. A system that was specifically engineered for the concentration of VOCs and SOx. Neutralized any harmful VOC’s to the environment in the most effective manner.
A large refinery in California needed vapor control on a propane recovery line. In order to stay within the permit, the refinery would have to degas the pipeline to accommodate the Bay Area AQMD limits. A quick and easy vapor control solution was needed. 600 pounds of VOC’s removed just under five hours.
A petrochemical company needed both vapor control, and degassing for a spherical 30,000 barrel Butadiene tank. Envent was able to quickly switch from a vapor control, to a degassing service with little to no downtime, and ahead of schedule.