A refinery contacted Envent to have a 150,000 barrel internal floating roof degassed for inspection. The tank contained gasoline, which has a high BTU/cubic foot, so a correctly sized thermal oxidizer is critical.
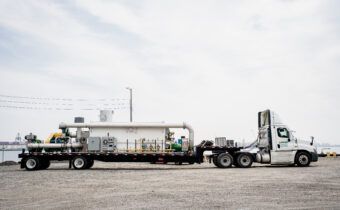
A refinery contacted Envent to have a 150,000 barrel internal floating roof degassed for inspection. The tank contained gasoline, which has a high BTU/cubic foot, so a correctly sized thermal oxidizer is critical.
A nationwide petroleum company had an API inspection deadline on a 110’ diameter External Floating Roof Tank containing sour crude product. There was an acute hazard in the tank for pyrophoric materials, materials which ignite in the presence of oxygen without an ignition source. The petroleum company understood that they would need an all-star team to degas, clean, and inspect this tank.
A terminal company in Texas City utilized a flare to control vapors on their storage tanks. When the flare failed, Envent was called to control excess vapors. Envent responded to this emergency, and was able to arrive onsite within four hours.
A Southern California refinery was operating a thermal oxidizer in the South Coast Air Quality Management District (SCAQMD) that registered a flow rate of 267 SCFM, exceeding the maximum permissible. Envent diagnosed the problem, procuring a new sensor and recalibrating the refinery’s equipment.
A large refinery in California needed vapor control on a propane recovery line. In order to stay within the permit, the refinery would have to degas the pipeline to accommodate the Bay Area AQMD limits. A quick and easy vapor control solution was needed. 600 pounds of VOC’s removed just under five hours.
A petrochemical company needed both vapor control, and degassing for a spherical 30,000 barrel Butadiene tank. Envent was able to quickly switch from a vapor control, to a degassing service with little to no downtime, and ahead of schedule.
An Oil and Gas terminal had mixed 350 BBL of product inside a pipeline. The company was going to push the mixed product to a LPG transport truck using a pig, and Envent was requested to control vapors on the truck to prevent it from overpressuring. Successfully purged the pipeline of the mixed product in 6 hours of operation.
A terminal located on the Northwest had to meet their deadline inspection on a large, 350,000 BBL Butane storage tank. They had a narrow window to complete the degas, turnaround work and return the tank back to service.
A 180,000 BBL Southern California refinery wastewater tank, frac tanks and centrifuge equipment needed vapor control and degassing during sludge removal. The two month long project needed redundancy and great attention to detail to abide by the permitting requirements. Maintained 24/7 operation while making the short generator service intervals.
A Houston ship channel refined product storage terminal requested our degassing expertise to engineer a solution for an unconventional sphere tank. Due to the unconventional design of the tank, previous attempts by competitors failed and the customers budget was blown. Other degassing contractors lack Envent’s engineering expertise and equipment.
A long-time customer has his project had been shut down when they witnessed flames leaping from the side manway of the tank – dragons. The benefit to the customer came in the form of Checks and Balances. When one company provides two completely different scopes of work, transparency to the customer can suffer.
An Illinois refinery required a 169,000-barrel overflow tank to be degassed. Estimated to have saved $250,000 by contracting Envent.