A refinery conducted a turnaround on a Hydrocracker unit in the Deer Park area, and they required a complete turnaround solution. Having worked with Envent before, the customer knew that we could solve all of their needs.
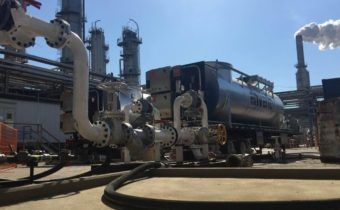
A refinery conducted a turnaround on a Hydrocracker unit in the Deer Park area, and they required a complete turnaround solution. Having worked with Envent before, the customer knew that we could solve all of their needs.
A refinery customer planned a turnaround for their Fluidic Catalytic Cracking Unit and was in need of turnaround service support. Because Envent has demonstrated the ability to help our customers meet the new, stricter emission limits imposed by the new Petroleum Refinery Sector Risk & Technology Review (RSR) regulations, the refinery knew they were getting the best.
Port Arthur refinery customer planned a turnaround for their 4 Drum Delayed Coker Unit. Due to the stricter emission limits imposed by the new Petroleum Refinery Sector Risk & Technology Review (RSR) regulations, the refinery needed Envent’s help.
Deer Park refinery facility required a flareless turnaround due to the new Petroleum Refinery Sector Risk & Technology Review (RSR) regulations. In order to remain in compliance and shorten the duration of the decommissioning phase, Envent was called upon to depressure the unit.
Port Arthur refinery customer had to complete a flareless turnaround involving their Hydrocracker Unit. Envent mobilized three EMECS-42 thermal oxidizers, two ESCRUB-6000 recirculating scrubbers, and all associated safety equipment to complete the decommissioning.
During a turnaround, an industrial gas company required vapor control on a Propylene tank and vacuum trucks. Once emptied, the tank was to be degassed and placed out of service. All Envent personnel are trained using state of the art VOC detection methods, and equipment to guarantee best results.
A Southern California Refinery needed to conduct maintenance activities on a number of connected process units. The goal was to complete several hot taps on each unit and cleaning to remove years of product buildup. Envent worked with a cleaning contractor to provide a turnkey solution for this large scale turnaround.
The challenge was to handle the vapor control for 250 frac tanks and the blow downs from the towers, columns, and vapors from the vacuum trucks. Envent’s 24 hour manned operation ensured the tank was degassed correctly and safely.
Project: Turnaround Support Services. Cost Savings: $150,000. Location: Gulf Coast Refinery.
A refinery’s primary flare for the onsite tank farm was being taken offline for emergency maintenance. Envent provided a thermal oxidizer capable of destroying vapors during this maintenance period. Client continued tank farm operations during the turnaround without shutting down.